In the fast-paced, ever-evolving world of business, the ability to anticipate and respond to customer demand is paramount. This is where demand planning steps into the spotlight, empowering companies to thrive in an increasingly competitive market. But what exactly is demand planning, and why should enterprise leaders care?
To shed light on this critical business function, we’ve enlisted the expertise of Tom Bond and Scott Sellers, Algo’s VP of Managed Services.
Demand Planning Explained
At its core, demand planning is a strategic process that involves forecasting future customer demand for products or services.
“It’s the lifeblood of any organization, helping them optimize their supply chain, improve customer service levels, reduce costs, and enhance overall operational efficiency,” says Tom Bond, Algo’s VP of Managed Services.
It’s more than just gazing into a crystal ball; it’s a systematic approach that combines data analysis, market insights, and collaborative planning to create a roadmap for the future.
Demand Planning vs Demand Forecasting
Figure 2: Demand Planning vs Demand Forecasting
Demand forecasting is like predicting the weather and conditions for a trip, while demand planning is utilizing that forecasting data to decide what to wear and whether to pack an umbrella,” explains Tom Bond, Algo’s VP of Managed Services.
Scott Sellers, adds, “Forecasting is about understanding the potential future, but demand planning is about shaping that future to your advantage. It’s where strategy meets execution.”
In essence, demand forecasting provides the raw material – the prediction of future demand. Demand planning takes that forecast and molds it into an actionable strategy, aligning it with broader business goals and constraints.
Sellers explains, “Demand planning bridges the gap between forecasting and execution, allowing businesses to meet customer expectations and maintain competitiveness in the market.”
The Enterprise Impact: Why Demand Planning is Your Competitive Edge
Demand planning isn’t just a task; it’s the beating heart of a thriving business. It unites teams across departments, aligning them with a shared goal: exceeding customer expectations while maximizing profitability.
Here’s how demand planning empowers businesses to not only survive but thrive:
- Customer Delight, Not Just Satisfaction: “By understanding true demand patterns, companies can ensure adequate inventory is staged at the right locations to fulfill orders quickly,” says Tom Bond, VP of Managed Services at Algo. This translates to consistently stocked shelves, ensuring customers find what they need when they need it – the foundation of lasting loyalty.
- Optimized Inventory: Too much inventory ties up valuable resources, while too little leads to missed sales opportunities. Demand planning strikes the perfect balance, avoiding both costly overstocks and damaging stockouts. Bond emphasizes, “Poor planning can lead to supply chain disruptions, backorders, stockouts, and customer dissatisfaction.” Demand planning is your shield against these costly disruptions.
- Streamlined Operations, Accelerated Results: Knowing what customers want is the key to operational efficiency. From production schedules to delivery logistics, every step is optimized. This means lower costs, faster time-to-market, and the ability to pivot quickly in a dynamic market.
- Data-Driven Decisions, Not Guesswork: Demand planning leverages data to uncover customer preferences and buying patterns. This data-driven approach enables smarter decisions about pricing, promotions, product launches, and inventory levels. As Tom puts it, “By studying demand signals, enterprises can detect emerging trends, popular product variations, and geographic sales patterns.” This enables companies to seize opportunities, tailor offerings, and stay ahead of the competition.
- Resilience in an Uncertain World: Unexpected events are inevitable. Demand planning equips businesses with the foresight to prepare for sudden demand spikes, supply chain disruptions, or unforeseen market shifts. This resilience is your insurance policy for maintaining smooth operations and steady profitability, even when the unexpected occurs.
Demand planning is not just about meeting demand; it’s about shaping it to your advantage. It’s a strategic weapon that empowers businesses to deliver exceptional customer experiences, optimize resources, and drive sustainable growth. In today’s competitive landscape, demand planning is not just important—it’s essential.
Real-World Demand Planning Triumph: Microsoft Devices Transformation
As a global technology leader, Microsoft faced significant challenges in managing its complex supply chain and forecasting consumer demand accurately. The company struggled with fragmented data sources, limited visibility into sales and inventory, and inconsistent data formats – all hindering their ability to effectively anticipate and respond to market fluctuations.
To overcome these hurdles, Microsoft partnered with Algo, implementing their AI-driven demand planning solution. Algo centralized data from various sources, providing a unified platform for sales and supply chain teams to access and analyze critical information. This streamlined approach empowered Microsoft to make data-driven decisions, optimize inventory levels, and improve overall operational efficiency.
The results:
- Sales Increase: A 4% boost in sales.
- Inventory Reduction: Weeks of supply reduced by 20%, with a significant decrease in markdown exposure.
- Productivity Gains: Streamlined processes led to notable improvements across the board.
- Shelf Availability Improvement: Stockouts reduced by an impressive 30%.
These improvements translated to substantial cost savings, improved customer satisfaction, and a more agile, responsive supply chain.
David Warrick, former Global Supply Chain General Manager & Innovation Officer at Microsoft, praised Algo’s solution, stating, “Algo not only listened, but they also took our feedback, understood our pain points, and then turned that into actionable insights. Algo helped us turn a problem into an opportunity in one of the toughest times for Supply Chain globally.”
Microsoft’s success story highlights the power of advanced demand planning to tackle complex supply chain challenges and drive significant business improvements.
Give it a full read to see the remarkable results.
The Demand Planning Journey: From Data to Action
Demand planning is a journey that transforms raw data into actionable strategies, ensuring businesses stay ahead of the curve and meet customer needs effectively.
- Data Collection and Analysis: “The foundation of demand planning lies in data,” emphasizes Scott Sellers, VP of Managed Services at Algo. This encompasses historical sales data, market trends, economic indicators, and even unconventional sources like weather patterns or social media sentiment. “Thorough analysis of this data reveals patterns, seasonality, and potential risks,” he adds.
Figure 2: Algo’s Demand Forecasting Dashboard
- Demand Forecasting: Armed with data insights, the next step is to forecast future demand. This involves selecting the most appropriate forecasting methods, ranging from simple time-series models to sophisticated machine learning algorithms. Collaboration across departments ensures a holistic view, incorporating diverse perspectives and expertise.
- Demand Plan Creation: “This is where the rubber meets the road,” Sellers remarks. The demand plan seamlessly integrates the forecast with business objectives, inventory constraints, and supply chain capabilities. It’s a living document, continuously updated and adapted as new information emerges.
- Collaboration and Consensus: Demand planning is a team sport. It demands collaboration and consensus among stakeholders across functions, from sales and marketing to operations and finance. Regular meetings and transparent communication ensure alignment and shared understanding of each team’s role in executing the plan.
Figure 3: Algo’s Dynamic Monitoring Dashboard
- Execution and Monitoring: Once the demand plan is finalized, it’s time to translate it into action. This involves adjusting production schedules, optimizing inventory levels, and refining marketing and sales strategies. “Continuous monitoring of actual demand against the forecast is crucial for identifying anomalies or deviations and making necessary course corrections,” Sellers advises.
Demand Planning: Challenges and Best Practices
Demand planning isn’t without its challenges. Market volatility, unforeseen disruptions, and data quality issues can all impact forecast accuracy. However, by adhering to best practices, businesses can overcome these obstacles and achieve demand planning excellence.
- Invest in the Right Tools: Utilize demand planning software that can handle large datasets, automate repetitive tasks, and provide real-time visibility into demand trends.
- Foster Collaboration: Encourage open communication and collaboration between different departments. Break down silos and ensure that everyone has a stake in the demand planning process.
- Embrace Agility: Be prepared to adapt your plans as circumstances change. The ability to pivot quickly is essential in today’s dynamic business environment.
- Continuous Improvement: Regularly review and refine your demand planning process. Seek feedback from stakeholders, analyze results, and identify areas for improvement.
By mastering the demand planning process and implementing these best practices, businesses can transform demand planning from a reactive function to a proactive strategic advantage. The result is a more resilient, customer-centric, and profitable enterprise.
Selecting the Right Demand Planning Software
Choosing the right software for demand planning involves aligning technology with your company’s unique needs. Consider factors like industry specificity, scalability, integration capabilities, user-friendliness, advanced analytics, and collaboration features.
- Industry Specificity: Does the software cater to your industry’s nuances? Look for solutions with pre-built models and industry-specific best practices.
- Scalability: Will the software grow with your business? Ensure it can handle increasing data volumes and complexity as your company expands.
- Integration Capabilities: Seamless integration with your existing ERP system and other data sources is crucial for accurate and timely demand insights.
- User-Friendliness: Intuitive interfaces and user-friendly workflows empower your demand planners to work efficiently and effectively.
- Advanced Analytics: Look for software with robust analytics and reporting capabilities to gain deeper insights into demand patterns and trends.
- Collaboration Features: Demand planning is a team effort. Choose software that facilitates collaboration and communication across departments.
Beyond the Basics: The Future of Demand Planning
While artificial intelligence (AI) and machine learning (ML) have undeniably revolutionized demand planning, the future holds even more transformative possibilities. The convergence of AI with other emerging technologies is paving the way for a new era of autonomous decision-making in demand planning.
Imagine a demand planning system that not only predicts future demand with unprecedented accuracy but also automatically adjusts inventory levels, optimizes pricing strategies, and even initiates marketing campaigns in response to real-time market signals. This isn’t science fiction; it’s the direction in which demand planning is rapidly evolving.
“The future of demand planning is not just about predicting demand; it’s about empowering AI to autonomously shape that demand,” states Tom Bond, VP of Managed Services at Algo. Scott adds that “These systems will optimize inventory, pricing, and marketing in real-time, liberating human planners to focus on strategic vision, ultimately fostering a more innovative, customer-focused, and profitable business ecosystem.”
The key to success will be to strike the right balance between automation and human oversight. While AI can handle the heavy lifting of data analysis and forecasting, human expertise will remain essential for interpreting insights, making strategic decisions, and ensuring that the system aligns with broader business goals.
The future of demand planning is not just about AI; it’s about harnessing the power of AI to create a more agile, responsive, and intelligent supply chain. By embracing this future, businesses can unlock new levels of efficiency, profitability, and customer satisfaction.
About the author
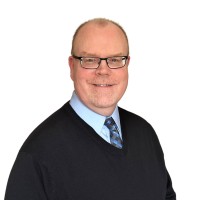
Scott Sellers
Scott is the Vice President of Managed Services at Algo. He is a seasoned leader with 20+ years of supply chain management experience in retail and omni channel environments. Scott has a demonstrated history of data driven decision making leveraging all available ERP, MRP, WMS, TMS, and inventory management systems to drive performance improvements.