In retail, accurately predicting what customers want—and when—isn’t optional. Demand planning drives balanced inventory, smooth supply chains, and on-time product availability. In fact, McKinsey reports that advanced demand planning can reduce inventory costs by up to 20% and boost forecast accuracy by 30–40%.
But here’s the catch: not all retail sectors are created equal. CPG brands grapple with short shelf lives and promotional spikes, while consumer electronics companies face rapid innovation and unpredictable product launches. Hard goods retailers, on the other hand, manage long product lifecycles, bulky inventory, and sensitivity to economic trends.
As Algo’s SVP of Solution Architecture, Sanjeev Balasubramaniam explains, the variability across sectors makes a one-size-fits-all approach ineffective:
“Each retail category brings its own volatility and that’s why demand planning can’t be standardized. The key is data-led customization.”
These unique challenges demand equally specialized strategies. A generic approach isn’t just inefficient, it’s risky.
This blog breaks down the key demand planning hurdles in CPG, consumer electronics, and hard goods, offering tailored, tech-enabled solutions for each. Whether you manage fast-turning SKUs or durable items, understanding sector-specific obstacles is the first step toward smarter, more resilient planning.
Demand Planning in the Consumer-Packaged Goods (CPG) Sector
Demand planning in the Consumer-Packaged Goods (CPG) industry is particularly challenging due to fast product turnover, frequent promotions, and constantly shifting consumer preferences. Even minor forecasting errors can lead to major financial setbacks. Here are four key challenges that make accurate planning in CPG uniquely complex:
1. Short Shelf Life
Many CPG products—especially perishables like dairy, produce, and ready-to-eat meals—have limited shelf lives. Overstocking leads to waste, while understocking results in lost sales and poor customer experiences. Accurate short-term forecasting is critical but often beyond the capabilities of traditional models.
2. Promotional Volatility
CPG brands rely heavily on promotions to drive volume. However, discounts, bundling, and seasonal campaigns can create sharp, unpredictable demand spikes. Without real-time insights and predictive tools, companies risk over- or underestimating promotional impact.
3. Supply Chain Complexity
The CPG supply chain spans multiple tiers—manufacturers, distributors, retailers, and global suppliers. Delays at any point, from port congestion to geopolitical disruptions, can cascade across the network. Managing inventory in such a fragmented system requires agility and real-time visibility.
4. Price Sensitivity
In inflationary conditions, consumers are more price-conscious than ever. Small price changes—whether from competitors or cost adjustments—can shift buying behavior quickly, demanding real-time response.
Solutions to Overcome Demand Planning Challenges in CPG
To address the fast-moving and unpredictable nature of CPG demand, companies must move beyond traditional forecasting and embrace smarter, integrated planning strategies. Predictive analytics can help fill gaps for new product launches by analyzing market trends and similar SKUs, allowing teams to plan more confidently despite limited historical data. Traditional spreadsheets fall short when it comes to reacting to real-time demand shifts.
“You can’t plan for the unknown with spreadsheets. AI lets CPG teams’ sense, predict, and act in real time—something legacy systems were never built to do.”
Sanjeev highlights how AI-powered tools close this gap by enabling CPG teams to sense and respond in real time.
Aligning production with marketing ensures inventory is ready when promotions hit, reducing excess stock and missed sales. At the same time, strong supplier partnerships offer better visibility and flexibility—crucial for navigating delays and disruptions in global supply chains. Finally, real-time demand sensing tools help brands adjust quickly to shifts in consumer behavior by tapping into POS data, social trends, and external signals.
Together, these strategies enable CPG brands to forecast more accurately, respond faster, and create a more agile, resilient supply chain.
Demand Planning Challenges in Consumer Electronics
Demand planning in the consumer electronics industry is uniquely complex, shaped by rapid innovation, product customization, and global supply chain dependencies. In a space where technology evolves fast and customer expectations shift just as quickly; accurate forecasting is both essential and difficult to achieve.
1. Rapid Innovation Cycles
Constant product updates and tech advancements shorten lifecycles and make older models obsolete quickly. This results in erratic demand patterns—spikes for new launches followed by sharp drop-offs—making traditional forecasting methods unreliable.
2. Customization Complexity
Electronics are offered in numerous variants—sizes, colors, storage capacities, and feature bundles. Forecasting at the SKU level across regions and channels increases complexity and can lead to mismatches in stock availability.
3. Global Supply Chain Risks
Electronics brands depend on globally sourced components like chips and sensors. Geopolitical risks, natural disasters, and trade restrictions can cause major delays. Long lead times limit flexibility, making real-time responsiveness critical.
4. Seasonal Surges
High-volume events like Black Friday and year-end holidays bring significant demand spikes. Without precise planning, retailers risk stockouts at peak times or excess inventory afterward.
Solutions to Overcome Demand Planning Challenges in Consumer Electronics
To manage the complexities of consumer electronics demand planning, companies must adopt agile, data-driven strategies. Predictive analytics can help forecast demand for new product launches by analyzing pre-orders, market trends, and past performance—minimizing the risk of over- or underproduction. Aligning production with marketing campaigns ensures inventory is available when demand spikes, maximizing both sales and promotional impact.
Strengthening collaboration with suppliers improves visibility into lead times and potential delays, enabling faster and more informed decisions. Meanwhile, demand-sensing tools provide real-time insights into consumer behavior which allow brands to adjust forecasts and shift inventory at the SKU level based on live sales and market signals. SKU-level demand sensing offers much-needed precision in a market dominated by product variations.
“Forecasting variant-level demand across channels is tough. That’s why SKU-level sensing tools are game-changers for electronics brands.”
Sanjeev underscores how this capability transforms forecasting for electronics brands.
Together, these solutions empower electronics brands to increase forecast accuracy, reduce inventory risk, and stay responsive in a fast-paced, innovation-driven market.
Demand Planning Challenges in Hard Goods (Durable Retail Goods)
Planning demand for durable goods—such as furniture, appliances, and home improvement products—presents a distinct set of challenges. These items typically involve higher price points, longer purchase cycles, and bulkier inventory, making forecasting more complex and long-term in nature.
1. Long Product Lifecycles
Unlike fast-moving goods, durable products have slower turnover and longer lifespans. Demand is irregular and harder to predict, as customers purchase these items infrequently. This makes inventory planning a balancing act. Overstocking ties up capital and warehouse space, while understocking risks lost sales and long lead times.
2. Macroeconomic Sensitivity
Demand for big-ticket items is closely linked to broader economic indicators like housing market trends, inflation, and interest rates. A surge in homebuilding might boost demand for appliances, while an economic downturn could cause demand to plummet. Forecasting models must incorporate these external factors to stay relevant.
3. High Storage and Logistics Costs
Large, heavy goods incur higher transportation and warehousing expenses. Inefficient storage or demand miscalculations can quickly drain resources and create costly bottlenecks.
4. Financing-Driven Purchase Behavior
For many customers, buying durable goods depends on access to credit or installment plans. Shifts in lending conditions can significantly influence sales volumes, making it harder to forecast demand without financial data.
Solutions to Overcome Demand Planning Challenges in Hard Goods
Overcoming demand planning challenges in hard goods requires a strategic mix of long-term forecasting, regional agility, and infrastructure optimization. Trend-based forecasting models that factor in historical data and macroeconomic indicators help retailers better anticipate slow-moving shifts in demand and plan more proactively over time.
To improve responsiveness and efficiency, retailers should localize inventory placement based on regional demand patterns and integrate financing data into their forecasts. Since purchasing behavior for big-ticket items often depends on credit availability, tracking installment trends and lending conditions can enhance forecast accuracy. Additionally, investing in modular, scalable storage solutions helps manage the high cost of storing bulky items, making operations more flexible and cost-efficient.
By combining these strategies, retailers can strengthen demand planning processes, reduce overhead, and stay better equipped to respond to changing market conditions.
The Role of Technology in Solving Sector-Specific Challenges
Technology is a cornerstone of effective demand planning, especially in sectors as varied as CPG, consumer electronics, and hard goods. From managing perishables to forecasting multi-variant product launches, today’s challenges require more than historical data and static models.
Data alone isn’t enough—retailers need systems that turn insights into aligned action. As Sanjeev notes:
“The most successful retailers don’t just use data—they connect it. Integrated planning platforms make collaboration and execution faster and smarter.”
Integrated systems align core functions like supply chain, marketing, and sales, giving teams a unified view of demand. With everyone working from the same real-time insights, retailers can adjust faster and respond more effectively.
Artificial intelligence and machine learning also play a key role. These technologies sift through vast amounts of live and historical data to detect market shifts, anticipate demand spikes, and deliver more accurate forecasts.
Real-time data access is critical too. Dynamic forecasting models that respond to consumer behavior, macroeconomic changes, and seasonality help retailers act in the moment—rather than reacting after the fact.
Together, these innovations transform demand planning into a proactive, sector-specific strategy that drives resilience and efficiency.
Lessons for Retailers: The Road Ahead
In today’s fast-evolving retail environment, there’s no longer room for one-size-fits-all strategies. Every product category—whether it’s fast-moving perishables, customizable electronics, or high-value hard goods comes with its own demand planning nuances. Retailers must shift from standardization to smart customization.
Resilient retailers distinguish themselves by adapting their planning strategies to suit each product category.
“The most forward-thinking retailers tailor their planning models to the nature of the product and the pace of the category. That’s how they stay agile while scaling.”
Resilience planning is now non-negotiable. Inflation, geopolitical tensions, and supply chain instability continue to challenge global operations. Retailers need demand planning systems that not only forecast accurately but flex with changing conditions—without compromising speed or service.
Sanjeev also pointed out the value of learning beyond your sector:
“Cross-industry knowledge sharing is underrated. What works in CPG may inspire innovation in electronics or hard goods. The key is knowing what to adapt and what to evolve.”
At Algo, we help retailers bring these lessons to life. With AI-powered forecasting, real-time insights, and connected planning tools, we empower businesses to move from reactive to strategic—forecasting smarter, responding faster, and building resilience for the future.
Discover how Algo can future-proof your demand planning strategy today.
About the author
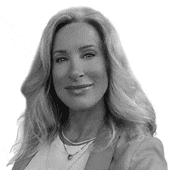
Karen McNaughton
Karen is the Vice President of Global Marketing at Algo, where she leads strategies to enhance brand awareness and demand generation for the company’s supply chain intelligence platform. With over twenty years of experience in senior marketing roles at various SaaS technology organizations, Karen brings extensive expertise in leading global marketing teams and executing go-to-market strategies.